Part 1 – Don’t map and improve parts of the end to end process
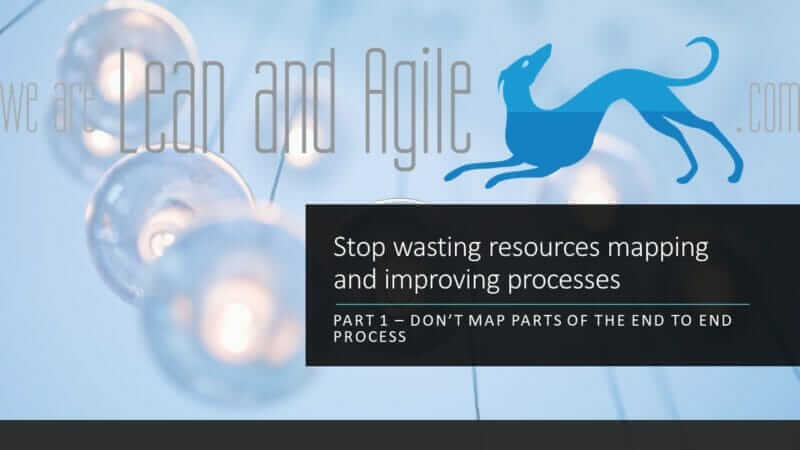
This is a very strange blog to write for someone who always recommends organisations map and understand their processes and look to improve them prior to looking for any technology and other solutions. Here we are asking you to consider not applying mapping techniques and continuous improvement. This has nothing to do with the tools you use it is purely about approach.
Don’t get me wrong I am not turning my back on my belief in the power of applying lean thinking to our processes, merely I am trying to encourage you to learn the lessons from many ‘failed’ improvement projects and programmes.
Practically every organisation we talk to in the public and private sector is trying to improve its processes. The drivers for improvement are different across the public and private sectors but the approach and outcomes are the same. We need to deliver more for less. We need to either grow our company or meet increasing demands with reducing resources or sometimes a combination of both.
We still believe in process mapping and process improvement but we want everyone to do it in the best possible way.
Why are you telling us to stop, have you gone mad? I thought you loved process mapping and improvement.
Here we are talking about a very specific set of circumstances around the approach to mapping and improvement that can only ever deliver sub optimal results. Having worked in organisations, as an improvement coach, as a consultant and lately as a supplier of improvement technology we have engaged with many organisations who have adopted this approach before realising its drawbacks. If you want to build a strong improvement programme you really want to get the foundations right.
As an external supplier we are rarely engaged in projects or programmes that are going well. We normally become involved because a project is not going well and maybe even close to being deemed a failure. There are a multitude of reasons for this but today we tackle the one that is very common and also almost certain to not deliver the results you expect or need. We are really lucky to be able to engage with so many organisations delivering improvement we are able to learn from many people’s experiences. This is a critical building block of any successful improvement strategy, programme or project.
What is it that you are talking about?
The internet is a wonderful place for resources but there is an awful lot of clickbait out there. By now I would be wondering if this was worth continuing to read or if it is just clickbait. So, I guess we best get on with it!
There are really 2 types of approach I would argue and demonstrate cannot be successful without some extreme good luck with other random factors turning in your favour (in which case it wasn’t actually your improvements delivering benefits anyway).
Approach 1 – Mapping and improving silos of an end to end process
This is a very common approach. I think it relates directly to how departments are managed and the targets they have. Each department involved in a process is very likely to be managed by different individuals. Regularly those individuals report into different senior managers. Each department has its own targets and outcomes it needs to deliver. Delivering those will define a manager as successful.
Processes cross multiple departments and often will not have a clear process owner i.e. someone who is responsible for ensuring the end to end process is delivered. When this is the case improving the end to end process can be an acrimonious and difficult process with each responsible manager chasing different business outcomes. Even perception of what customer value or needs are in each department can differ.
All of this may well contribute to why many organisations continue to try to make life easier by looking to improve the processes only within departmental silos. I think there is a clear logical argument why this can never deliver success. If you are doing this in your organisation please STOP WASTING YOUR RESOURCES.
Another driver for adopting this approach can be things like digital transformation or customer service improvement projects. These by their nature can isolate one area of the value stream/end to end process and seek to apply improvement there often in isolation.
Approach 2 – Mapping and improving an end to end process but in silos
This second approach is a variation on the theme, but this time you might think you have solved the first problem but in reality, you have not. We have mapped and modelled hundreds if not thousands of processes in our time. The most important element by far from a learning perspective is the capture of the As Is process (the current state). We believe the most important people to be in that workshop or workshops is the people doing the work. They have the most to give and the most to learn from the knowledge of how the end to end process currently works across silos.
This approach is all too common in our experience is to look to improve the end to end process. The knowledge and understanding of the end to end process is only gained by the business analysts. The other drawback of this approach is the lack of buy in by the stakeholders. Because they have not seen or understood the end to end process, they cannot help shape the solutions and nor are they very likely to buy in to the end results. Have a look here at how Toyota develop capabilities and focus on learning (this is hot off the press and the first time they have covered the topic also it was tweeted by Daniel T Jones)
https://planet-lean.com/lean-learning-toyota/
Let’s look at process mapping and process improvement in silos in more detail
Any mapping and improvement lean projects or programmes will generally be looking to deliver improvements and outcomes based on a purpose and an understanding of the customer and business value we need to deliver. We will then create the conditions where our people can look at the process and seek to deliver it in new ways removing waste along the way. If you want to understand more about the principles of lean have a look here
https://flevy.com/blog/14-principles-of-lean-toyota-production-system-tps/ or if you want to understand more about Purpose, People and Process try this blog
https://blog.kainexus.com/improvement-disciplines/lean/purpose-people-and-process-the-foundation-of-a-lean-organization
Let’s look at an example simple process – buying a parking permit
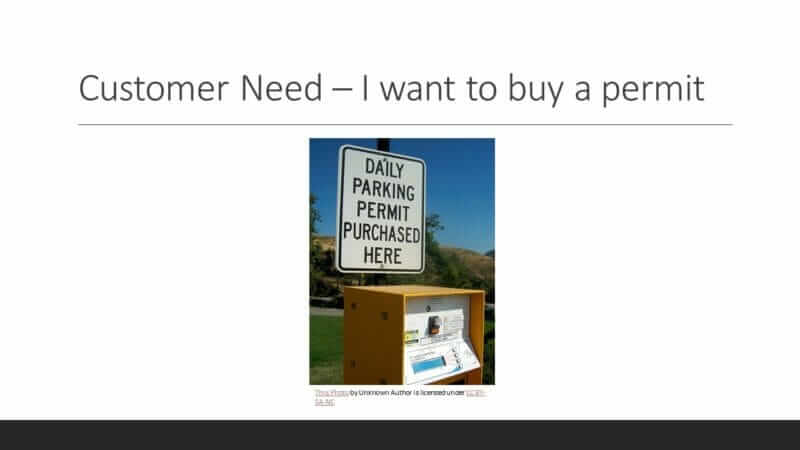
This is a hypothetical example and a deliberately simple process and value stream. I have chosen to involve 3 departments in the buying a parking permit process but there easily could be others depending on the type (HR could be involved if awarding it is job related, Payroll could be involved if the permit is paid through salary sacrifice). I have picked a more straightforward model with Customer Service, Car Parks and Finance involved in fulfilling the buy a parking permit process.
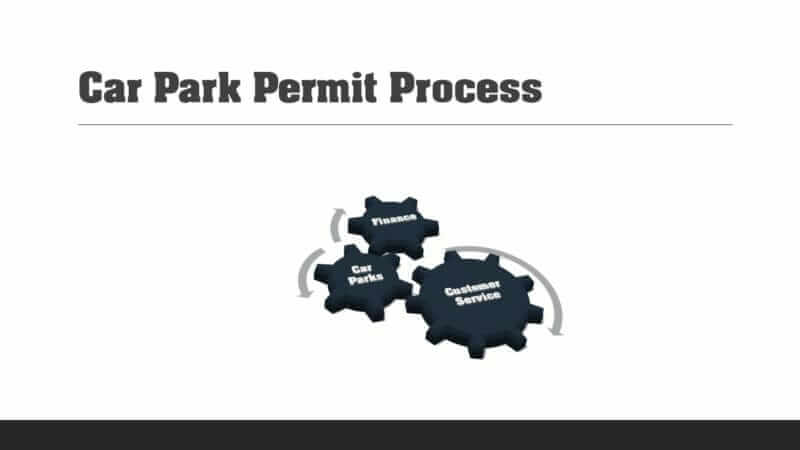
The process crosses the three departments in order to deliver the customer and business value in the transaction. It is very likely that a different manager is responsible for each department and also very likely that more than one senior manager is responsible for managing the managers.
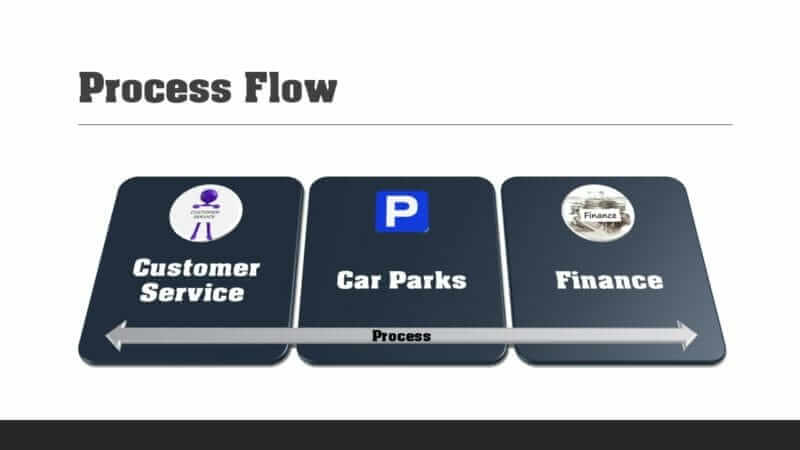
We may choose to map and improve one, two or all of the silos, but if we do it in silos, we can have up to three separate views of Purpose, People and Process driving the improvement and three different target outcomes in those silos. The purpose of improvement projects in customer service, car parks and finance are very unlikely to be the same. Each department has its own targets for savings and improvements.
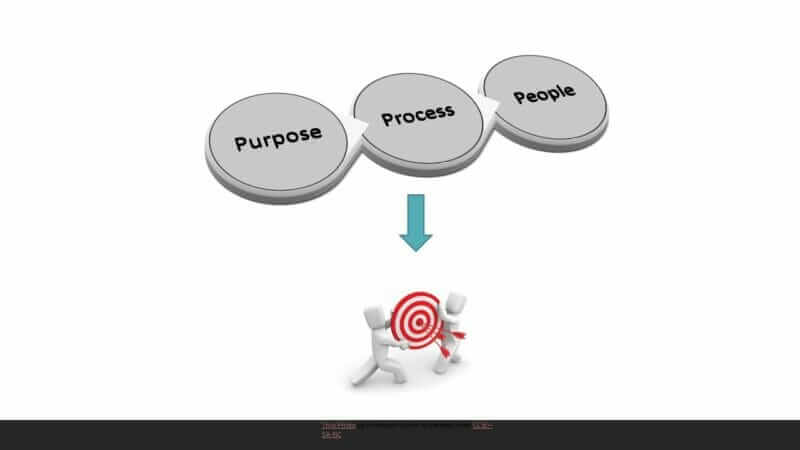
If we put that all together and look at optimising in silos this is what the model looks like.
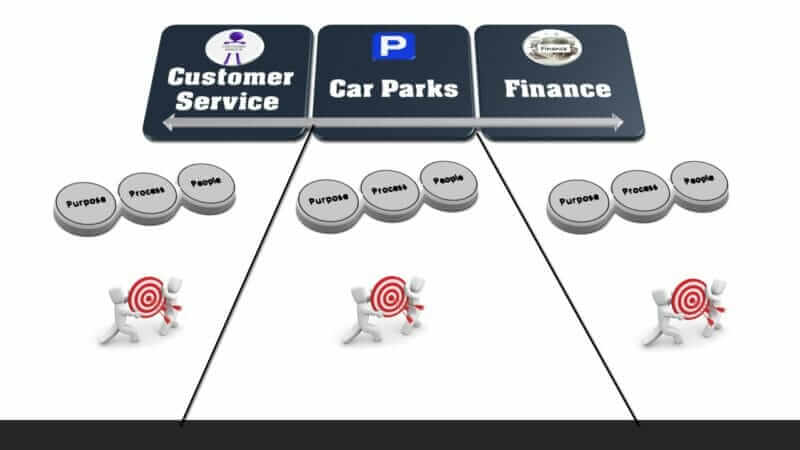
For me this approach is a primary reason why some ‘lean’ projects are deemed to be failures. If we consider how the organisation may report the outcomes of this and the benefits profile it is very likely that they would look at the identified benefits of each silo improvement would be added together and form the expected benefits of the three improvement projects. With this siloed approach to improvement the one thing I can absolutely guarantee is that first up it is a less efficient use of resources (three projects vs one) and that the sum of the identified benefits will absolutely not equal the total of the three benefit profiles.
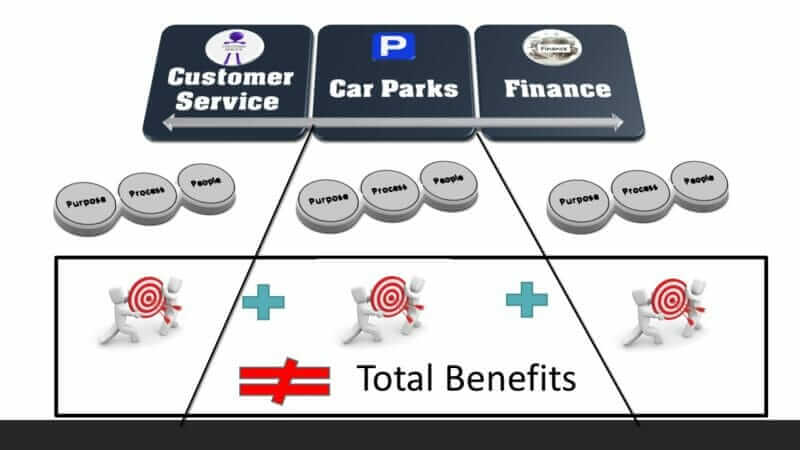
At its most basic level nothing has been done about optimising the end to end process. The most likely point in a process where under or over processing (therefore waste) comes in is when a process moves between roles or departments. In none of the 3 improvement projects will anyone have considered the disbenefits caused by the improvement ideas upstream or downstream in the process (it cannot as this has not been studied or considered). All benefits have been individually identified without netting off disbenefits.
One thing I can guarantee is that the total benefits will be substantially less than the total of the three. It is not unusual for there to be no net benefits and even sometimes net disbenefits (especially where only one area has been ‘optimised’).
Improving in silos is very likely to result in bad investments in ‘solutions’ to symptoms rather than causes.
Perceived failure leads to more waste in projects and programmes as we investigate why expected benefits were not realised.
Failure to deliver benefits increases the likelihood of Muda Muri and Mura in your processes as expected efficiencies fail to materialise however the reductions in staffing have occurred read more here
https://blog.toyota.co.uk/muda-muri-mura-toyota-production-system
What might be a better way?
- It is easier, faster and more resource efficient with one improvement project versus three.
- All stakeholders understand the end to end process and can help to improve it using their knowledge and skills.
- There can be a single shared organisational purpose rather than three operational purposes. The people use their knowledge and skills to improve the end to end process rather than silos.
- Benefits identified will consider the disbenefits in the end to end process and changes having a major negative upstream or downstream impact are less likely to be implemented.
- Everyone will be on the same page an understand the end to end process.
- You are less likely to invest in point solutions to a silos problem and more likely to be looking to invest in solutions that can optimise the full process.
- Benefits profiles are likely to be much closer to the likely outcomes.
- Chances of success of improvement projects and programmes are exponentially increased.
Why does this approach happen so regularly?
We understand why this approach can be seen as easier. The lack of process owners can make looking at end to end processes more difficult and looking at silos easier. The way managers are monitored and measured drives a siloed approach to improvement (if I am measured on delivering improvements in my department that is what I will aim to do).
Often projects target just parts of the process like digital transformation or customer service improvements. Sometimes it seems easier to take this path. Many practitioners raise this approach to us as sub optimal and ask us how they can change this. We have been involved in picking up many projects where this approach has been taken and now the pressure is on to deliver.
It genuinely is not easier because (and I hope you agree) looking at the model it cannot deliver the results we are all looking for in our organisations.
These and many other reasons are why we are creating this blog to hopefully help you to look at your approach and change it or at least to understand the disbenefits and to be able to plan for them and expect them.
We hope this blog can be used by the practitioners on the ground to raise the challenge around approach to improve the way you deliver improvement.
We work on many projects and programmes where we continuously learn about good and bad ways to deliver continuous improvement. Through experience we can say that this siloed approach has been demonstrated time and time again to deliver sub optimal results.
It is easy to change this and build your project or programme on a strong foundation. Hopefully this blog can help you start to address this issue in your organisations.
How do we improve our process improvement approach?
Our advice to you would be to try to change your approach from one that is focussed on optimising in silos to one that is focussed on improving the end to end process to deliver your organisations purpose.
There are huge benefits to delivering improvement on the end to end processes versus the silos. You can significantly reduce the risks of failures by adopting this approach. Improving the end to end process immediately reduces the effort required and improves your chances of delivering successful organisational outcomes. At its very base level focussing on the end to end process in this example would mean you focus on a shared outcome and purpose. You aim to use your people and knowledge to drive improvements in the end to end process.
What should we do to improve process improvement?
Please use this article to start the conversation about better ways to deliver process mapping. Let’s try to focus on organisation rather than departmental benefits. Let’s try to reduce rework and waste in our processes by getting improvements right first time.
What if that doesn’t work?
We are always happy to help organisations to get on a better path to continuous improvement. If you are still struggling get in touch and we are happy to help. If we can put you on a better path then it is likely you will want to optimise your approach even more which will mean talking to us about services we offer. If you need more help, we are happy to present our thinking to your wider organisation and help you move forward. We believe in delivering success for our customers and providing value add services.
What are the benefits to our process improvement projects if we do this?
Hopefully you can see the benefits of improving your approach are huge.
You can be more efficient and effective.
You can avoid waste and rework.
You can avoid ‘failure’ of your improvement projects.
You can deliver predictable achievable benefits.
You can gain trust and belief in your improvement programmes.
You can focus your development on improvements that will deliver.
You can engage your people in the redesign of your services.
You can do all of this without any investment in new technology.
You can create a strong platform to build from.
Please let us know what you think about this blog and please share with your peers hopefully we can help a number of organisations and people.
If you want to understand more about why its all about the benefits have a look at our
blog here